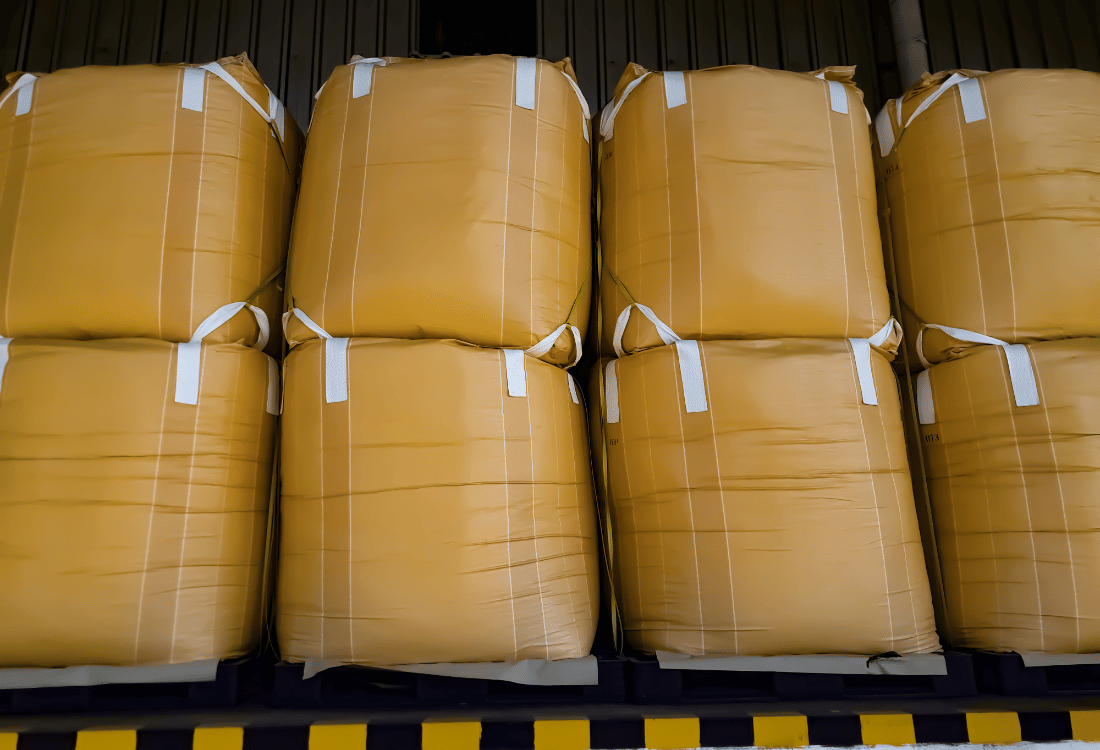
How Are Food Grade FIBC Bulk Bags Tested?
Gaining the certificate of approval for food grade products is a multi-stage process. There is good reason for this, because contamination at any stage can lead to serious and widespread consequences. Here’s the rigorous testing procedure that Food Grade Bulk Bags from Cliffe Packaging undergo before they reach our clients.
Manufacturing Environment
To meet stringent standards, the manufacturing facilities of Food Grade FIBC bulk bags must also be tested and certified. This certification is to ensure that aspects such as cleanliness, hygiene, pest control, and ventilation, are safe. The main organisation for this testing is the British Retail Consortium Global Standards (BRCGS).
The BRCGS has a five-stage certification process that culminates in a full audit. This must then be maintained by adhering to on-going compliance measures, which include fostering a safety culture, detailed reporting, and regular staff training.
Quality Control & Performance
Quality control is a multi-stage process carried out by the manufacturer, within the parameters outlined by BRCGS certification. Each bag is assigned a unique ID, which tracks it from raw material to the point of delivery. At Cliffe Packaging, our Food Grade FIBCs bags are manufactured in ‘clean room’ UV light conditions, using the latest in sterilisation technology.
They are vacuum air cleaned to remove fibres and are then scanned for contaminants such as metals. The FIBCs are finally packed in sterile conditions and placed on heat-treated ISPM standard pallets.
All FIBC bulk bags, including food-grade varieties, undergo rigorous performance testing to ensure durability, safety, and compliance with diverse applications. These tests simulate real-world environments and include:
- Top-Lift Tests: Evaluating strength under maximum load conditions.
- Compression Tests: Ensuring bags remain stable and intact when stacked.
These tests guarantee that every food-grade FIBC meets or exceeds safety and performance expectations.
Delivery
Following a technologically advanced manufacturing process, each bag undergoes multiple stages of rigorous quality testing. These tests are designed to ensure the bags meet the highest standards for food safety and performance.
Once manufacturing is complete, meticulous attention is paid to the delivery process to maintain this high standard. The FIBCs are loaded onto heat-treated pallets, which are specifically prepared to prevent contamination and comply with international hygiene regulations. These pallets are then placed into containers that have undergone thorough inspections to ensure they are entirely free of debris, pests, or any other contaminants.
To guarantee the integrity of the delivery, the doors of these containers are sealed with security tags, providing an additional layer of protection against tampering during transit. This final stage ensures that the hard work and dedication put into manufacturing and testing our Food Grade FIBC Bulk Bags culminate in a safe, clean, and reliable product.
Next Steps
For the highest quality and rigorously tested Food Grade FIBC Bulk Bags, Cliffe Packaging has an extensive catalogue paired with a reputation for excellence. To learn more, speak to a bulk packaging expert today.
Image Source: Canva